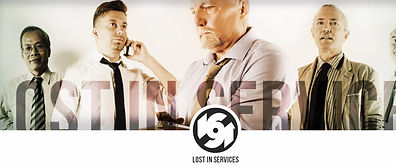

INTRODUCTION
The topic of business process improvement or reengineering has a long history in business literature both on the academic side and among managers, there is a lot of confusion and debate on this topic and it has not lost its popularity. The concept of reorganizing dysfunctional business processes still exists even in the twenty-first century – usually with new and more sophisticated tools and methodologies, but based on old principals. The narrowing markets, increasing competition and the recent economic crisis all stimulate companies towards continuous rationalization, cost reduction and increased efficiency to gain some kind of comparative advantage which creates a basis for the development of methodologies for process improvement.
For almost two decades now there has been considerable discussion and even debate in the literature as well as among managers on the role, substance and interdependence of process “regenerative” or “amelioration” techniques, methods, strategies and constitutes of these issues. Despite this long and deep debate there still remains much confusion amongst researchers and even experts. However there is a consensus on the need for the improvement of business processes as the basis of the competition has moved from cost and quality to flexibility and responsiveness. The value of process improvement is now being recognized in gaining sustainable competitive advantages, yet there is a serious lack of adapting these methods within service industries.

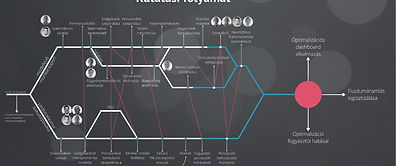
FLUID FLOW AND LOGISTIFICATION
Nowadays’ economic trends have gone through significant changes over the last century for. Production and service activities have become faster and more easily available. This change is due to the globalization, which is basically a political-economic process, in which the strongest actors of world economy standardize and generalize political and economic rules based on their own interests through major international institutions.
National borders have blurred as a result of globalization. Both production and service processes, including distribution will no longer be confined within borders. With the development of transportation and the revolution of information technology inaccessible areas have become potential markets. Globalization has accelerated the flow of information, which able to operate business and financial processes faster and better than ever. In this market environment, large companies quickly seized the opportunity to develop and extend their processes to obtain huge market share.
The internationalization of services is different from the globalization of products. In the case of service activities only the uniform systems can be transposed to countries with different cultures. The most difficult task of globalization of services is bridging the cultural, demographic and behavioural differences. However, two basic models definitely have successfully accomplished this difficult mission and become contemporary a major determinants in services and production.
Studying a process in logistical aspect means analysing the flow of information, materials, resources or emissions and in this regard it can be modelled, either by mathematical or information technology methods. If it is possible to contemplate a service process from a logistical point of view, the previously available assessments, modelling and simulation methods could be transferred to them after a counterpart tuning. [1] Therefore, hereinafter by the logistification of service processes or by any other not clearly defined process we mean the analyse of the flow of materials, information, etc. through the processes. In order to do that, we briefly introduce relevant global service models.
LOGISTIFICATION
The logistical aspect analysis of processes shall provide assistance when we are not curious about what the elements of the processes do or how they work in sequences, but about the connections and cooperation of the processes of the whole system as well as the observation of the flow of materials related to processes (certificates, documents, components, semi-finished products, or the people themselves, or any other abstract elements such as information, etc.).
This type of substance flow can be found processes of all systems, such as the patients’ flow in a hospital requires the same examination as the contract documents systemic movement of a bank. Of course, this would be a very simplistic way of analysing processes. It has become also very important to analyse the information flow which takes part in the same time and in a competing way with the substance flow. Sure in many cases, these two basic processes cannot be separated, because a paper-based order is a substance in its own and information as well.
Reviewing the above processes cannot be examined individually or isolated in a system, they have to be analysed together, their effect have to measured simultaneously, and thus no longer shall be distinguished material, substance or information (etc.) flow process, it is enough just to talk about process, and thus their handling will be uniform. Hereinafter we mean by logistification the temporal and spatial changes and changes in related data of the processes of any kind of system as well as the combined modelling and analysis in terms of efficiency, sensitivity and optimality. The generalized substances, materials, information (etc.) flowing in the processes shall be called fluid.
MODELING
Manufacturing and service companies differ mainly in the communication and interaction with customers. It would still result in a new approach, that in case of production firms’ corporate activity produce tangible, clearly identifiable and manifested goods. [2] It is also very often, that service companies are trying to establish cultures based on frequent interactions. As a consequence of this attitude 'moment of truth' experiences multiply and front office employees will face with increased conflicts. [3]
The global market expansion of standardized is called McDonaldization, based on Ritzer. [4] The system in this case follows the work organization principles of Fordism and Taylorism. The company acquire competitive advantage from the productivity cost-benefits. The service providers standardize their processes so the output of the output is constant and always equal to the consumers' expectations. In this case the higher volume of sales is crutial to reduce costs. This provides comparative advantage for the company. Consumers have pretty much and accurate information on the standard service due to advertisements, their own and their acquaintances experiences. McDonaldized business processes can be repeated and thus problems and errors arising in business activity can be effectively solved. However, the reparability assumes the existence of trust, meaning that the provider will not commit an error again. The operating logic of McDonaldization as a system is basically divided into four dimensions: efficiency, predictability, reliability and control by technology.
